Professional solutions on concrete addtives, Concrete Foaming Agent, Superplasticizer, CLC Blocks Additives, and foaming machine
Introduction: The Transformation of Concrete Through Chemical Innovation
Concrete, the cornerstone of modern construction, has evolved beyond its traditional role as a load-bearing material. Today, innovations in concrete foaming agents—chemical additives that introduce air voids into fresh concrete—are enabling the production of lightweight, insulating, and sustainable materials like cellular lightweight concrete (CLC). Among these additives, cellular concrete foaming agents and CLC foaming agents stand out for their ability to optimize concrete’s density, thermal performance, and cost-efficiency. This blog explores the technical nuances of these foaming agents, contrasts them with alternative air-entraining technologies, and dissects the economic factors shaping concrete foaming agent prices. By unraveling these dynamics, we empower builders, engineers, and manufacturers to make informed decisions in the quest for greener, smarter concrete solutions.
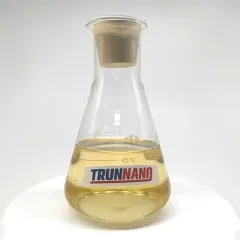
Cellular Concrete Foaming Agents: The Science Behind Lightweight Structures
1. Definition and Mechanism
Cellular concrete foaming agents are synthetic or protein-based surfactants designed to generate stable, uniform air bubbles when mixed with water and cement paste. These bubbles form a cellular matrix within the concrete, reducing its density by 30–80% compared to conventional concrete. The resulting cellular lightweight concrete (CLC) offers exceptional thermal insulation, fire resistance, and acoustic damping, making it ideal for non-structural applications like void fills, roof insulation, and precast panels.
2. Key Advantages
- Thermal Insulation: CLC’s air voids create a low-conductivity matrix, with thermal resistivity (R-value) up to 5 times higher than standard concrete.
- Weight Reduction: Densities as low as 300 kg/m³ enable lighter foundations, reduced shipping costs, and easier handling.
- Fire Safety: The inorganic composition and cellular structure resist temperatures up to 1,200°C, meeting ASTM E119 fire-rating standards.
- Workability: Foaming agents enhance pumpability, allowing CLC to be cast into complex molds or sprayed onto vertical surfaces.
3. Limitations and Considerations
- Strength-to-Weight Trade-Off: While lightweight, CLC’s compressive strength typically ranges from 0.5–15 MPa, limiting its use to non-load-bearing applications.
- Shrinkage and Cracking: Excessive air content may increase drying shrinkage, necessitating additives like shrinkage-reducing agents or fiber reinforcement.
- Durability in Aggressive Environments: Protein-based foaming agents may degrade in acidic or saline conditions, requiring synthetic alternatives for marine or industrial settings.
4. Comparative Analysis: Cellular Foaming Agents vs. Traditional Air Entrainers
- Against Vinsol Resin: While vinsol resin (a natural air entrainer) improves freeze-thaw resistance, it lacks the bubble-stabilizing properties needed for CLC production.
- Against Aluminum Powder: Aluminum powder reacts with cement alkalis to generate hydrogen gas, creating voids but posing safety risks (flammability) and inconsistency in bubble size.
CLC Foaming Agents: Tailoring Performance for Specialized Applications
1. Definition and Composition
CLC foaming agents are a subset of cellular concrete additives engineered for high-performance CLC. These formulations often blend synthetic polymers (e.g., sodium lauryl sulfate, SLS) with stabilizers (e.g., hydroxypropyl methylcellulose, HPMC) to ensure bubble longevity during mixing, placing, and curing. Advanced CLC foaming agents may incorporate biodegradable components or nanomaterials to enhance rheology or fire resistance.
2. Key Advantages
- Bubble Stability: CLC-specific foaming agents produce bubbles resistant to coalescence, ensuring uniform pore distribution and density control.
- Density Precision: Manufacturers can adjust formulations to achieve target densities (e.g., 400 kg/m³ for roof screeds vs. 800 kg/m³ for structural infill).
- Environmental Compatibility: Many CLC foaming agents are free of formaldehyde or volatile organic compounds (VOCs), aligning with green building standards like LEED.
- Compatibility with SCMs: CLC foaming agents work synergistically with supplementary cementitious materials (SCMs) like fly ash or slag, reducing cement content and carbon footprint.
3. Limitations and Considerations
- Cost: High-performance CLC foaming agents may cost 2–3 times more than generic air entrainers, though density reductions offset material expenses.
- Mix Design Sensitivity: CLC requires precise water-to-cement ratios and foaming agent dosages; deviations can lead to collapse or segregation.
- Curing Sensitivity: CLC’s open pore structure necessitates moisture-retentive curing (e.g., wet burlap, plastic sheeting) to prevent premature drying.
4. Comparative Analysis: CLC Foaming Agents vs. Aerated Autoclaved Concrete (AAC) Additives
- Against Aluminum Paste (AAC): AAC relies on aluminum powder and high-pressure steam curing, while CLC foaming agents enable ambient curing, reducing energy costs.
- Against Preformed Foam Systems: Preformed foams (e.g., generated by foam generators) offer precise control but require additional equipment, whereas CLC foaming agents integrate directly into the mix.
Concrete Foaming Agent Price: A Market Analysis of Cost Drivers and Value Propositions
1. Factors Influencing Pricing
- Raw Material Costs: Synthetic foaming agents (e.g., SLS-based) are typically cheaper than protein-based or nanocomposite formulations.
- Production Scale: Bulk manufacturers benefit from economies of scale, offering lower per-unit costs than boutique suppliers.
- Performance Specifications: High-stability, low-shrinkage, or fire-resistant foaming agents command premium pricing.
- Geographic Variations: Regional demand, import tariffs, and transportation costs (e.g., shipping liquid foaming agents overseas) inflate prices in some markets.
2. Price Ranges Across Product Types
- Entry-Level Foaming Agents: Basic SLS-based formulations cost 1.50–3.00/kg, suitable for low-strength CLC in residential projects.
- Mid-Range CLC Foaming Agents: Polymer-stabilized blends with HPMC or biodegradable components range from 3.50–6.00/kg, balancing cost and performance.
- Premium Specialty Agents: Nanoparticle-enhanced or fire-retardant foaming agents exceed $8.00/kg, targeting high-end commercial or industrial applications.
3. Comparative Cost Analysis: Foaming Agents vs. Alternative Lightweighting Methods
- Against Expanded Polystyrene (EPS) Beads: EPS beads cost 0.50–1.20/kg but require additional mixing equipment and may compromise fire safety.
- Against Pumice or Perlite Aggregates: Lightweight aggregates cost 0.30–0.80/kg but increase batching complexity and reduce workability.
- Against Foamed Glass Gravel: Recycled glass foams cost 2.00–4.00/kg but offer lower thermal resistivity than CLC.
4. Total Cost of Ownership (TCO) Considerations
- Material Savings: A 50% reduction in concrete density can cut material costs by 30–40%, offsetting higher foaming agent prices.
- Labor Efficiency: CLC’s pumpability reduces placement time by 20–50% compared to traditional lightweight concrete.
- Lifecycle Costs: CLC’s durability and thermal efficiency lower heating/cooling expenses and maintenance over 50+ years.
Selecting the Right Foaming Agent: A Decision Framework for Practitioners
1. Application-Specific Requirements
- Thermal Insulation: Opt for CLC foaming agents with microbubble stability (e.g., HPMC-stabilized) for roof or wall panels.
- Fire Resistance: Choose phosphate-based or nanoclay-enhanced foaming agents for tunnel linings or fire barriers.
- Structural Loads: Use low-air-content (e.g., 40–50% porosity) CLC foaming agents for infill blocks in precast systems.
2. Environmental and Regulatory Compliance
- VOC Limits: Select water-based, low-odor foaming agents for indoor applications (e.g., renovations).
- LEED Credits: Prioritize biodegradable or recycled-content foaming agents to earn Innovation in Design points.
- Waste Management: Opt for liquid foaming agents with non-hazardous disposal protocols to minimize environmental impact.
3. Supplier Evaluation Criteria
- Technical Support: Ensure suppliers offer mix design guidance, on-site training, and troubleshooting for foam collapse or segregation.
- Quality Certifications: Verify compliance with ASTM C869 (foaming agent standards) or EN 12350-10 (European concrete testing).
- Supply Chain Resilience: Partner with suppliers with global distribution networks to mitigate regional shortages.
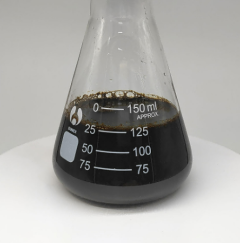
The Future of Foaming Agents: Innovation and Sustainability Trends
Emerging trends in foaming agent technology are reshaping the CLC landscape:
- Bio-Based Formulations: Algae-derived surfactants or casein proteins reduce reliance on petrochemicals, aligning with circular economy goals.
- 3D-Printed CLC: Nanoclay-reinforced foaming agents enable printable CLC with isotropic strength, ideal for disaster relief housing.
- CO₂-Cured CLC: Carbon-negative curing processes (e.g., mineralization of CO₂ into calcium carbonate voids) enhance sustainability credentials.
Conclusion: Optimizing CLC Performance Through Strategic Additive Selection
The choice between cellular concrete foaming agents, CLC foaming agents, and alternative lightweighting solutions hinges on balancing technical performance, economic viability, and environmental stewardship. While synthetic foaming agents offer affordability and scalability, premium CLC formulations unlock unparalleled control over density, durability, and fire safety. Meanwhile, concrete foaming agent prices reflect not just raw material costs but also the value of innovation in bubble stability, compatibility with SCMs, and lifecycle efficiency. As the construction industry prioritizes decarbonization and resilience, the evolution of foaming agents will continue to redefine the boundaries of concrete’s capabilities—proving that the future of building materials is as much about what’s left out (air voids) as what’s put in (cement).
Supplier
Cabr-Concrete is a supplier under TRUNNANO of Concrete Admixture with over 12 years of experience in nano-building energy conservation and nanotechnology development. It accepts payment via Credit Card, T/T, West Union and Paypal. TRUNNANO will ship the goods to customers overseas through FedEx, DHL, by air, or by sea. If you are looking for Concrete Foaming Agents, please feel free to contact us and send an inquiry. (sales@cabr-concrete.com)
Tags: cellular concrete foaming agent, clc foaming agent, concrete foaming agent price