Professional solutions on concrete addtives, Concrete Foaming Agent, Superplasticizer, CLC Blocks Additives, and foaming machine
Approximately 6,000 years ago, ancient Egyptians used quartz sand and natural soda ash or potassium carbonate produced during combustion to manufacture sodium silicate or potassium silicate. It is widely believed that the chemical composition of the frescoes preserved in the ancient cities of Pompeii and Herculaneum after the eruption of Mount Vesuvius in 79 AD is alkali metal silicate. In the 16th century, alchemists seeking the “philosopher’s stone” discovered that sand and potassium carbonate fused in a furnace to form sparkling water glass.
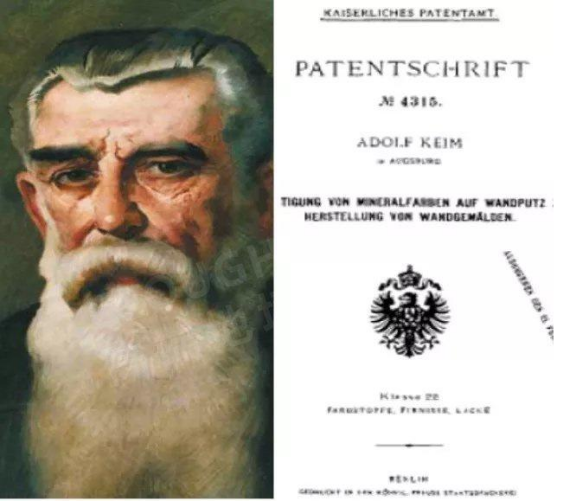
Although there are numerous references to water-soluble silicates in the literature, their practical application did not begin until 1825, under the leadership of Professor Fox, a mineralogist at the University of Munich. He conducted pioneering research and systematically studied the production methods of water glass, which he referred to as water-soluble sodium silicate and potassium silicate. He also proposed that water glass could be used as an adhesive, cement, and fireproof coating, as well as for sealing porous stone and as a base material for mural coatings. Commercial production of water glass began in Europe and the United States in 1855.
King Ludwig I of Bavaria was deeply impressed by the vibrant lime frescoes in northern Italy and desired to experience such artistic works in his Bavarian kingdom. However, the harsh weather north of the Alps quickly destroyed these artistic creations. Therefore, he issued an order to the Bavarian Academy of Sciences to develop a coating that resembled lime frescoes but was more durable. Scientist Adolf Wilhelm Keim used water glass as a binder to experiment with silicate paint. After years of extensive experimentation, he finally achieved successful results, applying for the first patent for inorganic silicate paint in 1878 and commencing production of silicate paint. To this day, KEIM FARBE Coatings Company (known as Mineral Brand Coatings in China) is named after him. KEIM FARBE Coatings Company is one of the world’s most renowned manufacturers of inorganic silicate coatings.
The first generation of inorganic coatings invented by Kem over 140 years ago was pure inorganic silicate paint (Pure silicate paints). It is a two-component coating (also known as 2K coating) composed of a powder mixture of inorganic pigments and fillers, and a liquid component of potassium silicate. According to the German standard DIN 18363, Section 2.4.1 on silicate coatings, its formulation consists of two components, contains no organic components whatsoever, and is only suitable for coating the surfaces of solid, absorbent mineral substrates. Since the late 19th century, the first generation of inorganic coatings has been widely used in architectural coatings in Europe. Its excellent weather resistance and color fastness remain unmatched. Buildings decorated with inorganic silicate coatings in the 19th century are still well-preserved today, such as the “White Eagle” Hotel in Stein on the Rhine River in Switzerland, the town hall in Schwyz, and the exterior facades of buildings in Oslo and Trondheim in Germany. While the first generation of inorganic coatings is still in use today, its drawbacks include being a two-component system that requires thorough mixing before use and a certain period of curing time.
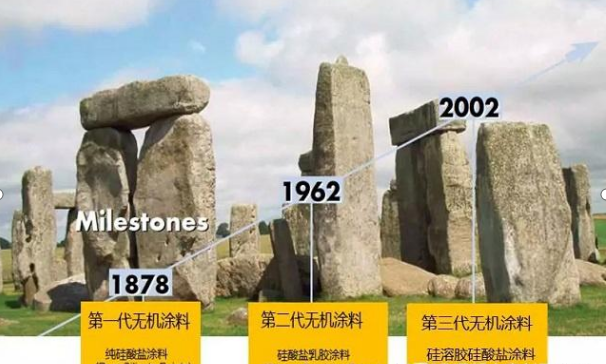
With the long-term experience of the exceptional weather resistance of 2K inorganic silicate coatings, and the appeal of newly emerging organic latex coatings—which are easy to produce, have excellent storage stability, and are convenient to apply—the market has sought a single-component packaging solution that combines the advantages of both inorganic and organic coatings. In 1962, the second generation of inorganic silicate coatings was introduced. It is a single-component silicate emulsion coating (Silicate Emulsion Paints), also known as organic silicate coatings (Organo-silicate paints), formulated using potassium silicate as the primary binder, supplemented with a small amount of high-alkali-resistant organic synthetic emulsion, and incorporating appropriate amounts of inorganic pigments, fillers, and additives. According to German standard DIN 18363, Section 2.4.1, the organic content (including emulsion and additives) of silicate emulsion paints must not exceed 5%. With the emergence of the second-generation inorganic coatings, since the 1970s, inorganic coatings in the form of silicate emulsion paints have gained significant popularity among consumers and have seen substantial development worldwide, particularly in Europe.
In 2002, the emergence of third-generation inorganic coatings brought about a revolutionary change in the exterior wall coating market: Based on a new adhesive concept, “sol-silicate paints” have opened up entirely new application areas for inorganic coatings. This new binder is a stable mixture of sol-silicate and potassium water glass. In addition to forming chemical bonds with inorganic mineral substrates through silicification, it also exhibits strong adhesion to robust organic coatings, making it suitable for almost any common substrate surface. The organic content of sol-silicate paints remains below 5%, thereby meeting the requirements of DIN 18363 for silicate latex paints.
From the first to the third generation of inorganic coatings, three significant milestones in development have been widely recognized by the global coatings industry. With the advancement of inorganic coating technology, new varieties continue to emerge. In 2013, German-based KEIM FARBE introduced the fourth generation of inorganic coatings suitable for wood surfaces; in 2018, a Malaysian inorganic coating company in Kuala Lumpur launched their fourth-generation inorganic coating—a silicate hybrid inorganic coating for exterior walls designed for tropical marine climates with heavy rainfall.
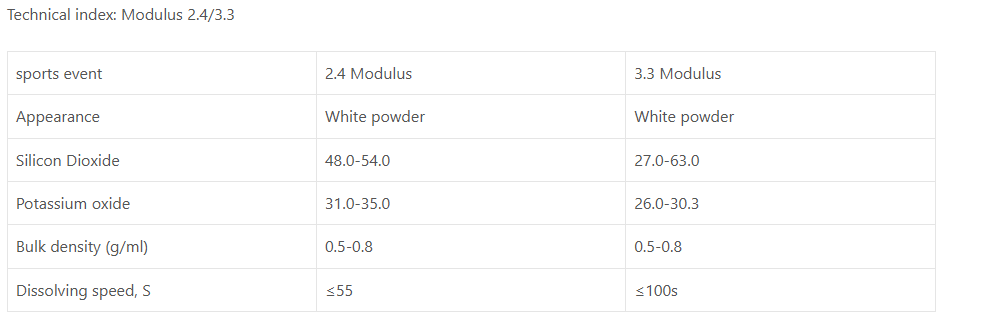
Inorganic silicate coatings now account for 10-15% of the water-based architectural coatings market in Europe and have also achieved significant growth in the architectural coatings markets of the United States, Asia, and Oceania.
Since the early 1980s, China has also reported research on inorganic coatings, with domestic development of several types of inorganic coatings using sodium silicate and potassium silicate as film-forming agents. However, the main types of coatings widely applied in engineering projects in China are synthetic resin emulsion exterior wall coatings modified with silica sol and two-component exterior wall coatings with potassium silicate as the primary film-forming material. In addition to ordinary decorative exterior wall coatings, functional inorganic wall coatings have also seen significant application and development, with primary types including inorganic anti-mold coatings, inorganic thermal insulation coatings, inorganic anti-condensation coatings, and inorganic fire-resistant coatings. Although the advantages of inorganic coatings are widely recognized in China, synthetic resin emulsion coatings remain the dominant product in the building coatings market. Research and application of inorganic silicate coatings are still limited, and there is a significant gap compared to developed countries in Europe and America.
In recent years, the international construction market has seen mandatory requirements for fire-resistant and non-combustible interior wall coatings in underground enclosed spaces, coupled with growing demand in the home decoration market for low-VOC, low-preservative, environmentally friendly interior wall coatings. These factors have driven the development of inorganic interior wall coatings. Major architectural coatings manufacturers are actively engaged in R&D for inorganic architectural coatings and continuously launching new products, presenting inorganic silicate coatings with a rare development opportunity and fostering the emergence of specialized inorganic coatings manufacturers. It is believed that inorganic silicate architectural coatings will become the next hotspot in the architectural coatings market, following natural stone coatings and water-based multi-color coatings.
Company Profile
Cabr-Concrete is the global leader in Low-Density Cellular Concrete (LDCC), Celluar Light Concrete (CLC), and advanced engineered foam solutions. Known globally for its commitment to research, innovation, and applied expertise, we have been providing engineered foam solutions since the early 2012’s.
We can supply polyethylene fibre (PVA fibre) all over the world. We have a professional technical department and quality supervision department, a well-equipped laboratory with advanced testing equipment and an after-sales customer service centre. Please send us an email or click on the required product to send an enquiry.
If you would like more information about sodium silicate or potassium silicate, please feel free to contact us at sales1@cabr-concrete.com.